What is a die cut machine do?
An automatic die cutting machine is a device used to cut out shapes, designs, and patterns from various materials such as paper, cardstock, fabric, and vinyl. It works by using metal dies or electronic cutting blades to precisely cut through the material, creating intricate and precise shapes. Automatic Die Cutter are commonly used in crafting, scrapbooking, and design projects to create custom shapes and designs for various purposes such as greeting cards, invitations, decorations, and more.
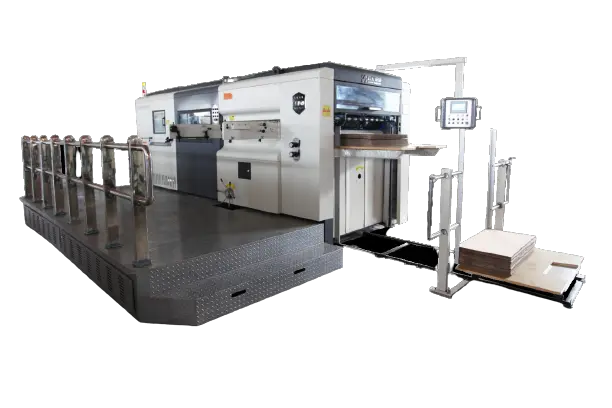
What Is The Flatbed Die Cutting machine Process?
The flatbed die cutting process involves using a flatbed die cutting machine to cut and shape materials such as paper, cardboard, foam, fabric, and other substrates. Here's an overview of the process:
1. Design and Preparation: The first step involves designing the desired shape or pattern to be cut. This can be done using specialized software or by creating a physical die or cutting template.
2. Material Setup: The material to be cut is placed on the flatbed of the die cutting machine. It is important to ensure that the material is properly aligned and secured to prevent shifting during the cutting process.
3. Die Placement: A custom-made die, which is a sharp steel blade in the shape of the desired design, is placed on top of the material. The die is precisely positioned to ensure accurate cutting.
4. Cutting Process: The flatbed die cutting machine applies pressure to the die, which then cuts through the material, creating the desired shape or pattern. Some machines may also use a combination of cutting and creasing to create more complex designs.
5. Removal and Finishing: Once the cutting process is complete, the cut pieces are removed from the material. Depending on the specific requirements, additional finishing processes such as scoring, perforating, or embossing may be performed.
Flatbed die cutting is commonly used in industries such as packaging, printing, and manufacturing to create custom shapes and designs for products such as boxes, labels, gaskets, and more. It offers precision, speed, and versatility in producing a wide range of cut designs.
What is a die cutter used for?
A die cutter is a versatile tool used for cutting various materials into specific shapes, designs, and patterns. It is commonly used in crafting, scrapbooking, and manufacturing industries for a wide range of applications. Some common uses of a die cutter include:
1. Crafting and Scrapbooking: Die cutters are popular among crafters and hobbyists for cutting paper, cardstock, and fabric into intricate shapes and designs for creating greeting cards, invitations, decorations, and other craft projects.
2. Packaging and Labeling: In manufacturing and packaging industries, die cutters are used to create custom shapes and designs for packaging materials, labels, and stickers. This includes cutting materials such as cardboard, foam, and adhesive-backed sheets.
3. Leatherworking and Textiles: Die cutters are used in the production of leather goods, textiles, and garments to cut precise patterns and shapes for items such as bags, shoes, clothing, and accessories.
4. Industrial Applications: In industrial settings, die cutters are used to cut materials such as gaskets, seals, and insulation into specific shapes and sizes for use in machinery, equipment, and construction.
5. Prototyping and Model Making: Die cutters are used in product development and prototyping to create precise and consistent shapes for mock-ups, prototypes, and models.
Overall, die cutters are valuable tools for creating custom shapes and designs with precision and efficiency across a wide range of industries and applications.
1.jpg)
1.jpg)
What is the difference between laser cutting and die cutting?
Laser cutting and die cutting are two distinct methods used for cutting materials, each with its own advantages and applications. Here are the key differences between the two processes:
1. Cutting Method:
- Laser Cutting: Laser cutting uses a high-powered laser to melt, burn, or vaporize the material along a predetermined path. The laser beam is guided by a computer-controlled system to cut through the material with precision.
- Die Cutting: Die cutting uses a sharp, custom-made metal die or cutting blade to physically press and cut through the material, creating the desired shape or pattern.
2. Versatility:
- Laser Cutting: Laser cutting is highly versatile and can cut a wide range of materials, including metal, wood, plastic, fabric, and more. It is particularly well-suited for intricate and detailed designs.
- Die Cutting: Die cutting is commonly used for cutting materials such as paper, cardboard, foam, fabric, and thin plastics. It is ideal for creating consistent shapes and patterns in large quantities.
3. Setup and Tooling:
- Laser Cutting: Laser cutting requires minimal setup and tooling, as the cutting path is controlled by software and does not require physical dies or templates.
- Die Cutting: Die cutting requires the creation of custom dies or cutting templates for each specific shape or design, which can involve initial setup and tooling costs.
4. Speed and Production Volume:
- Laser Cutting: Laser cutting is generally faster than die cutting for small to medium production runs, especially for complex designs and shapes.
- Die Cutting: Die cutting is well-suited for high-volume production runs, as it can efficiently cut multiple layers of material simultaneously using a single die.
5. Edge Quality:
- Laser Cutting: Laser cutting produces clean, precise edges with minimal material distortion, making it suitable for applications where edge quality is critical.
- Die Cutting: Die cutting can produce clean and consistent edges, but the quality may vary depending on the material and die used.
In summary, laser cutting offers versatility and precision for a wide range of materials and intricate designs, while die cutting is efficient for high-volume production runs of specific shapes and patterns in materials such as paper, fabric, and thin plastics. Each method has its own strengths and is chosen based on the specific requirements of the project.
Post time: Mar-22-2024